Każdy zna pojęcie spawania metali, ale co w sytuacji, gdy proces okazuje się trudniejszy niż zakładano ze względu na rosnące wymagania, takie jak redukcja przepaleń czy nadpaleń?
Lutospawanie zapewnia możliwość łączenia spełniającego wysokie wymagania jakościowe.
Lutospawanie – jak wygląda proces?
Lutospawanie metali w osłonie gazu obojętnego jest hybrydą lutowania twardego oraz spawania. Sprzęt i sposób jego obsługi jest identyczny jak podczas spawania metodą MAG/MIG. Jako gaz osłonowy stosuje się gaz obojętny, najczęściej czysty argon (ARCAL™ Prime).
Zalety lutospawania
Dzięki lutospawaniu można osiągnąć następujące rezultaty:
- uzyskanie szczelnych lutospoin,
- lutospoiny często nie wymagające obróbki,
- łączenie nie powodujące uszkodzenia powłok,
- utrzymanie właściwości antykorozyjnych,
- elementy z minimalną ilością odprysków czy odkształceń,
- możliwość łączenia materiałów różnoimiennych,
- większa wydajność w porównaniu do lutowania.
W dalszej części omówione zostaną bardziej szczegółowo zalety lutospawania.
Utrzymanie odporności na korozję dzięki lutospawaniu
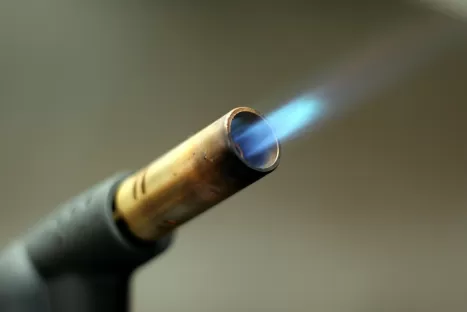
Jedną z zalet lutospawania w osłonie gazu obojętnego jest to, że temperatura topnienia lutu jest znacznie niższa od temperatury topnienia blachy. Dzięki temu blacha nie zostaje nadtopiona. Powierzchnia po przeciwnej stronie spoiny pozostaje bez zmian, takich jak przepalenia.
Ponadto przy lutospawaniu występuje niższe wnikanie ciepła. W większości przypadków wytrzymałość na rozciąganie jest absolutnie wystarczająca i spełnia oczekiwane wymagania w zakresie naprężeń. Lutospawanie w wytwarzaniu karoserii samochodów ma więc ogromną przewagę nad spawaniem, gdzie minimalizacja odkształceń stanowi główne wyzwanie. Obróbka wykańczająca połączeń po procesie lutospawania jest znacznie łatwiejsza i szybsza, ponieważ lut ma mniejszą twardość, co wpływa na szybkość szlifowania.
Jeśli nie mogą Państwo zmieniać właściwości chemiczno-fizycznych blach, a tym samym chcą Państwo zapobiec wypalaniu się składników stopowych, wówczas lutospawanie (w osłonie gazu obojętnego) będzie odpowiednią metodą.
Lutospawanie jako rozwiązanie do łączenia blach ocynkowanych
Blachy stalowe poddane procesowi ocynkowania stają się w znacznym stopniu odporne na korozję. Chcą Państwo połączyć blachy ocynkowane i obawiają się, że mogą one utracić właściwości antykorozyjne? Podczas spawania zawsze wyparowuje warstwa cynku, która powoduje utratę właściwości antykorozyjnych w miejscach spoin oraz ich najbliższej okolicy.
Ponieważ temperatura podczas lutospawania nie jest tak wysoka jak podczas spawania, warstwa cynku nie jest zniszczona. Parowanie warstwy ocynkowanej znacznie wpływa również na powstawanie niezgodności spawalniczych w spoinach w postaci zaporowań. Przy lutospawaniu powstawanie tych niezgodności jest ograniczone ze względu na ograniczone parowania cynku. Duża część ocynku pozostaje na powierzchni blach. Ponowne cynkowanie nie jest już konieczne, ponieważ blachy mają wystarczającą ochronę przed korozją.
Redukcja odprysków w przypadku lutospawania
Podczas spawania blachy ocynkowanej pojawia się problem dużej ilości odprysków spawalniczych przywierających do spawanej blachy. Ponadto przywierające odpryski spawalnicze uszkadzają ocynkowaną powierzchnię wytwarzając ogniska korozji. Przy lutospawaniu prawie nie ma odprysków, które mogłyby uszkodzić ocynkowaną powierzchnię i doprowadzić do pogorszenia właściwości antykorozyjnych. Dzięki temu procesowi można wyeliminować dodatkowe operacje mające na celu odtworzenie właściwości antykorozyjnych łączonych elementów.
Lutospawanie w osłonie gazów aktywnych
W niektórych przypadkach, aby wpłynąć na proces lutospawania zamiast osłony z gazów obojętnych można wykorzystać gazy aktywne. Niewielki dodatek dwutlenku węgla lub tlenu do gazu osłonowego może zminimalizować ilość wytwarzanego ciepła lub wpłynąć na prędkość wykonywanego procesu. Skład chemiczny osłony gazowej przy lutospawaniu powinien zostać dobrany indywidualnie do wymagań jakie ma spełnić wykonywany element.
Lutospawanie jest świetnym rozwiązaniem w zakresie łączenia wielu różnych rodzajów materiałów. Minimalizacja ciepła, redukcja zniekształceń, mniejszy odprysk i możliwość zachowania właściwości powłok naniesionych – to bardzo dobre argumenty przemawiające za tym procesem.